“Money for old rope” is an idea that easy money can be made from selling something that has been used and discarded. It implies there’s value in something that many consider worthless.
But what if it could also describe a forward-looking manufacturing strategy that combines reduced waste and lower carbon emissions with increased profits and customer retention? What if the “old rope” could be made good as, or better than, new?
This is a question that many of today’s manufacturers from heavy construction equipment to disposable drug delivery devices are taking increasingly seriously. Demand from customers, users, environmental groups, regulators and governments is forcing manufacturers to take another look at what happens to their products once users have finished with them. Pictures of your valuable branded products in landfill appearing in online forums is embarrassing, but can also drive demands from major customers that you do something about it. In healthcare, an understanding that discarded medical products are a leading cause of pollution-related deaths, and the NHS declaration that they intend to hand suppliers the responsibility for waste medical products, could mean that doing nothing could cost you customers.
As always, the intentions are laudable but the question is “what can we do?” The Circular Economy, Remanufacturing, Recycling, Refurbishing and “sustainable design” all describe aspects of the same core idea – giving your product a second, third or fourth life after its initial use. There is a hierarchy of these ideas based on the “residual value” of a used product, with material recycling – grinding up old plastics to make playground equipment – close to the bottom and “remanufacturing” – returning a product to its original condition and selling it (with warranties) – at close to its original value – close to the top.
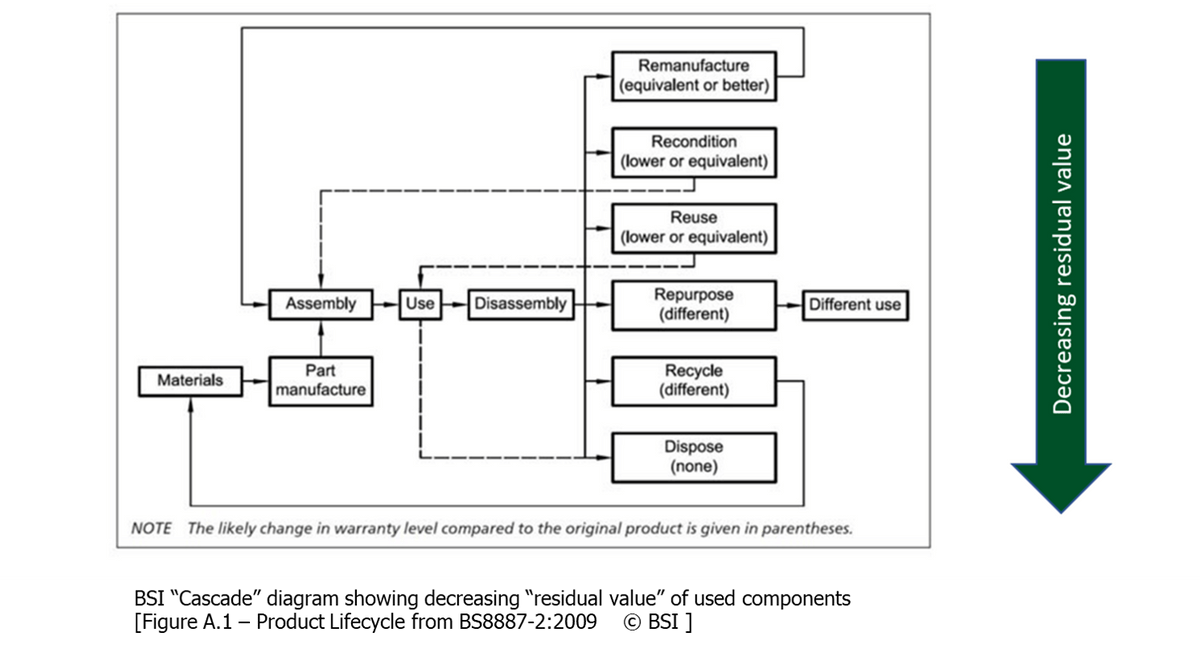
The question for industry now is, how to make this economically sustainable. If the intention is for your product to last many times longer, how do you consider that in the design and in your design specification? In the cost? In what you can recover? How do you then design a re-usable “core” to be used many times, perhaps with sacrificial parts that are subject to wear, contamination and damage? And if there’s value to be recovered, how do you manage that as a business? Some manufacturers recover and remanufacture their own products. Some 3rd party remanufacturers recover and remanufacture products they have had no stake in manufacturing. The good news for UK PLC is that we appear to be leading the thinking on this. A recent shift in medical product design regulations in the MDR and MHRA guidelines has led to the acceptance that medical products can now be remanufactured – but in a limited, managed way and with the same burden of proof on safety and traceability that applies to new products. The Ellen Macarthur Foundation leads thinking on the Circular Economy and the BSI has led ISO, EN and is now working with the Standardization Administration of China on how to implement remanufacturing approaches that work for business.
In Aladdin, “New lamps for Old” shows another familiar example of the hidden value in used products. Maybe we should get used to thinking this way about “old rope”.
Cormac O’Prey runs Kestrel Technology Consulting, a company specialising in medical device, smart energy and sustainable product design. He is is a long-standing member of the BSi committee for BS8887: Design for Manufacture Assembly, Disassembly and End of Life Processing